We detected, that your browser supports another language than the called one. This page is also available in your language! Would you switch to this page in your language?
SHARPENING AND MACHINING PCD ROTARY TOOLS OPTIMALLY
Efficient high-precision machining is the key to the production of PCD rotary tools.
PCD (polycrystalline diamond) is a synthetically produced diamond cutting material, which can be used for machining wood, plastic and metal. The material is mainly characterized by a high degree of hardness and abrasion resistance and is therefore important in industrial manufacturing processes.
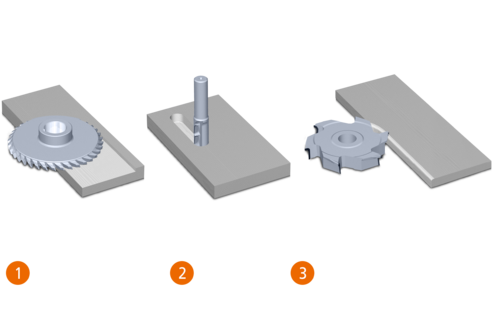
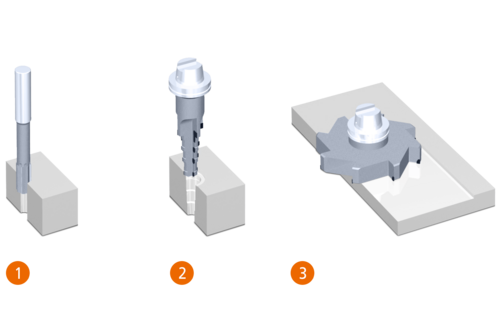
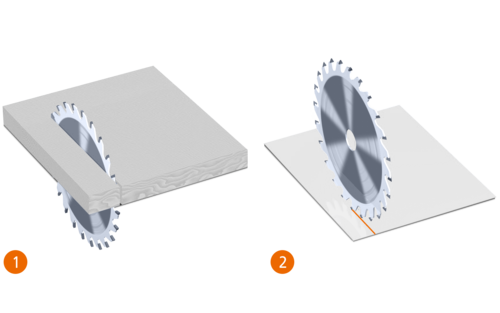
There are basically three types of eroding processes for polycristalline diamond rotary tools: Sink erosion, wire erosion and disc/rotary erosion.
Wire erosion and disc/rotary erosion work according to the same erosion principle and achieve the best results in terms of precision and surface quality.
However, there are differences in the shape of electrodes and their use. Therefore, some cutting edge shapes can only be machined by one of these two processes, e.g. no tooth sides can be eroded with the wire erosion process, as this requires the finest contours and radii (both on the outside and inside).
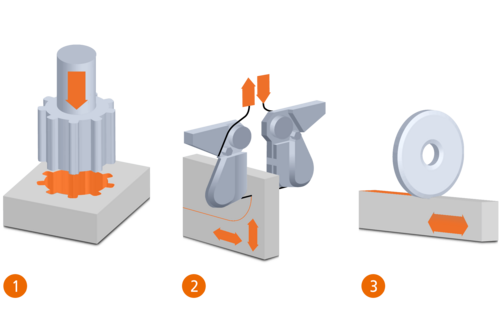
In order to determine the position and size of the PCD cutting edges, a fully automated measurement of the workpiece clamped in the machine is carried out before each erosion operation. To do this, one point per cutting edge is specified for the eroding machinery. The machine then scans several points on the cutting edge automatically in accordance with the set value. Even complex profiles can be measured in this way.
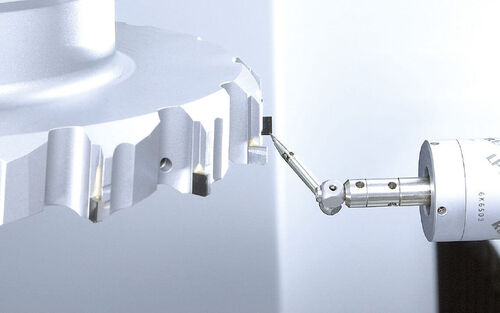
Eroding wire is used as an electrode during wire erosion. Copper and copper alloys are most suitable for this. Some of these wires are also coated with a layer of zinc, which results in better cutting power for certain materials.
Electric discharge removal takes place between the continuously self-renewing wire electrode and the polycrystalline Diamond cutting edge with very minimum clearance. The wire electrode is guided along the tool using two prisms aligned with the cutting edges. The small radius of the wire allows to produce up to 0.1 mm radii on the tool.
This results in the finest of contours and profiles.
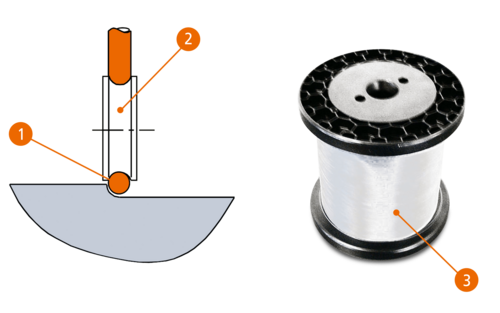
During disc/rotary erosion, removal takes place between the rotary electrodes and the PCD cutting edge with the most minimum of clearance.
Copper alloys are the most suitable for use in electrodes. However, the electrode should be easily machined to faciliate dressing the disc electrodes.
In order to distribute the wear of the electrode over the biggest area possible and to keep its geometry constant for as long as possible, the disc performs a rotational motion during erosion. The rotary electrodes are clamped and dressed directly on the machine. This results in optimal concentricity as the dressed tool is attached directly inside machine. The advantage of disc erosion is that both the circumference and the end face of a rotary electrode can be used for erosion, and the flank surfaces can therefore also be machined.
Discover the possibilities:
DISC EROSION MACHINES FOR COMPLETE MACHINING OF PCD-TIPPED TOOLS.
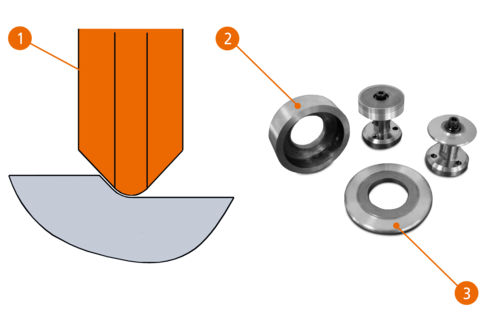
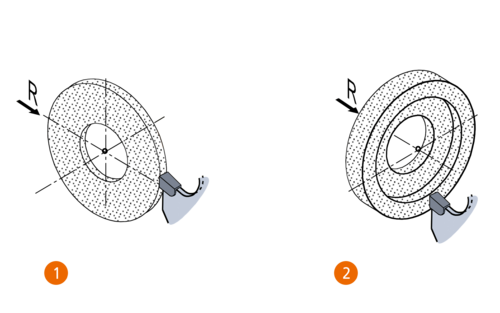
Projection measurement: The requirements regarding the accuracy of tools are extremely high. This is why there are measuring machines that project an image of the tool onto a screen. The measurements are displayed across the traverse path of the tool with the help of a measuring computer.
Optical measurement: In order to accurately determine the tool diameter, you need to measure with a camera or laser. The accuracy of this process is in the region of 1/1000 mm.
Surface measurement: The surface can be measured with a skidded gage or guided measuring system. Probe systems check the surface for both roughness and waviness: a diamond with a tip of 2 µm probes across the surface and records the smallest surface irregularities on the workpiece. When measuring surfaces on polycrystalline diamond plates, “Ra” stands for the roughness value. The cutting edges of PCD-tipped tools are visually assessed: New technology makes it possible to assess the surface and cutting edge quality using high-resolution cameras.
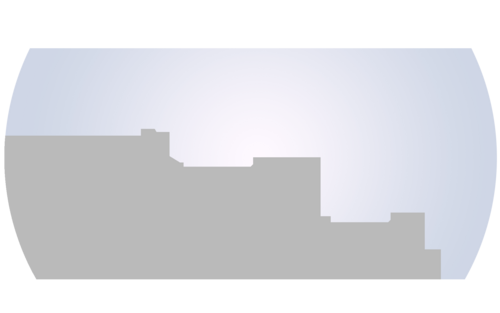
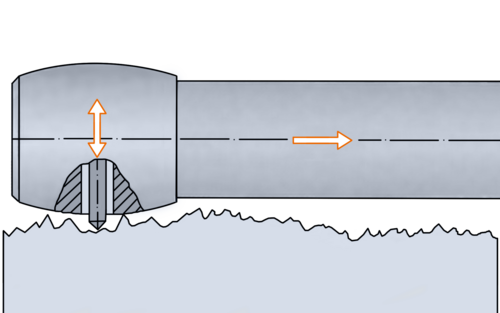
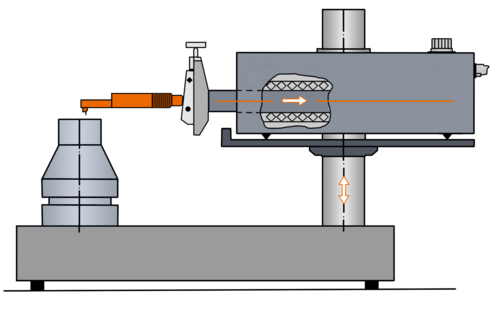
Every day at VOLLMER, we are engaged in extremely intensive work with the profiles, cutting edges and complex geometries of modern PCD rotary tools. We therefore constantly do research and test new technologies in order to continue optimizing our machining and manufacturing processes. We are happy to share our expertise in the form of targeted advice, and offer products which are precisely adjusted to particular requirements.