We detected, that your browser supports another language than the called one. This page is also available in your language! Would you switch to this page in your language?
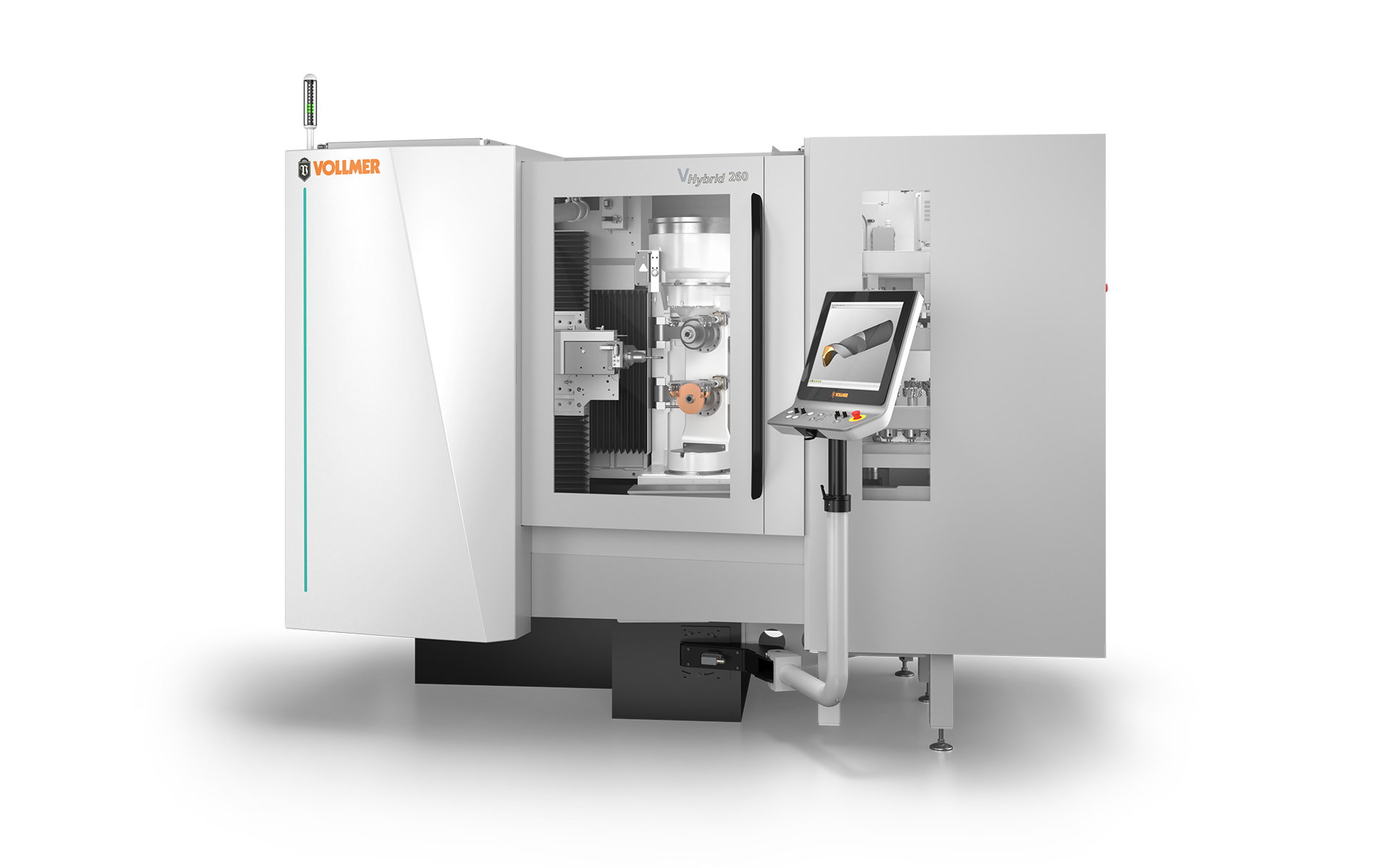
WALL CONCEPT
Very rigid, compact construction with optimal accessibility and overview for the operator.
MULTI-LAYER MACHINING
Grinding spindle and eroding spindle (bottom) are positioned vertically in the pivot point of the C axis. The result: Reduced machining times thanks to shorter linear-axis travel distances.
MODERN CONTROL-PANEL CONCEPT
Height-adjustable, with touchscreen, 19" diagonal screen size and optimum view into the machining chambers.
SOFTWARE
ExLevel Pro and VStandard for a comprehensive range of tools for drills and milling cutters. For greater flexibility and variety.
8-WAY CHANGER
Even greater flexibility for your production processes. Space for eight HSK 50 grinding and eroding wheel sets.
AUTOMATION
Such as with the HC 4 or the HC 4 plus for increased capacity and flexibility.
The word hybrid is derived from the Greek description for something that is bundled, crossed or mixed. In engineering, it describes a system which skilfully combines two technologies and therefore offers the best of both worlds. The combination of sub systems can give rise to brand-new positive features.
This is the case with the VHybrid 260 from VOLLMER, which combines the strengths of an innovative grinding machine with a powerful erosion machine – and makes it possible to switch between both functions in next to no time. The VHybrid delivers noticeably increased efficiency and profitability when machining rotary carbide and PCD tools with diameters of up to 150 mm.
Altogether that makes for two hundred per cent VOLLMER efficiency and profitability.
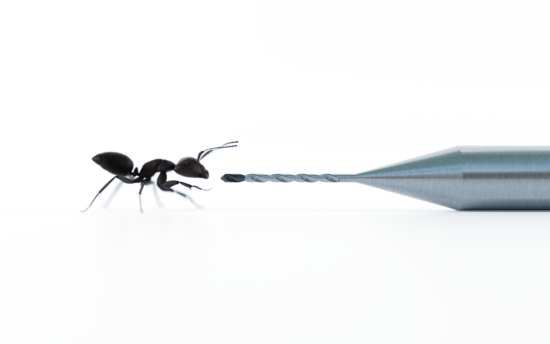
ERODING IN THE LIMIT RANGE
The VHybrid 260 is the only hybrid machine on the market that meets the high requirements for the production of PCD micro tools. Thanks to the innovative Vpulse EDM generator, the smallest microtools with diameters of 0.45 millimetres and below can be produced with the highest precision, performance and surface finish.
Machining of microtools: Find out more here
GRINDING AND ERODING ON A DIFFERENT LEVEL
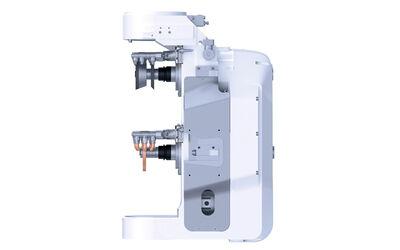
Innovative VOLLMER multi-layer machining with two spindles, automatic grinding and eroding wheel replacement is the key to the complete integration of two important tool machining processes. The ingenious arrangement of the grinding and electrode wheel is set precisely in the pivot point of the C axis ensuring you always achieve perfect results.
- TOP SPINDLE: GRINDING
Efficient machining of carbide tools with diameters of up to 150 mm (depending on the tipping, the machine kinematics also allow for larger diameters). Different automation options are available.
- BOTTOM SPINDLE: GRINDING AND ERODING
Powerful machining of carbide or PCD tools up to 150 mm thanks to the high-performance and finely tuned Vpulse EDM erosion generator (depending on the tipping, the machine kinematics also allow for larger diameters). A range of automation options are available here too.
The machine concept
For perfect grinding processes, the VHybrid 260 uses the innovative and proven principles of the successful VGrind 360, the world's first grinding machine with two vertically arranged grinding spindles. To avoid inefficient re-tooling processes, the bottom spindle of the VHybrid 260 has been equipped with a fully-fledged erosion unit. At its core is the Vpulse EDM erosion generator, which sets new benchmarks in terms of efficiency and surface quality.
CARBIDE GRINDING
- Five-axis CNC grinding machine with innovative kinematics. Short linear-axis travel distances and swivel ranges for increased efficiency and precision in production
- The vertical spindle arrangement solves the well-known problems related to fixed and floating bearings
- Grinding wheel in the pivot point of the C axis – for ultra-precise grinding results
- Innovative wall concept with the highest possible rigidity and outstanding damping thanks to polymer concrete
- Effective motor and spindle cooling concept for higher thermal stability and lasting power and precision
As a fully-fledged grinding machine, the VHybrid 260 can produce and sharpen carbide drills and milling cutters with a diameter range of up to 150 mm (depending on the tipping, the machine kinematics also allow for larger diameters).
- High flexibility due to the option of automatic grinding wheel replacement with integrated calibration and wear control
- Meaningful automation options for efficient and flexible production
EROSION OF PCD
- Maximum efficiency for reduced machining times
- Best surface and cutting edge quality: Finest, ultra-precise erosion pulses enable surfaces up to a roughness of 0,05 μRa, depending on the tool type
- Simple dressing of the erosion electrodes thanks to dressing device
- High process reliability across all grades of PCD
With its outstanding kinematics, the VHybrid 260 is ideal for machining rotary tooling with a diameter of up to 150 mm (depending on the tipping, the machine kinematics also allow for larger diameters).
- Precise electrode calibration and wear control for perfect erosion results
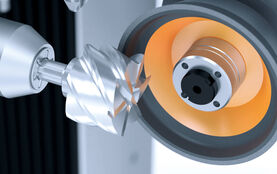
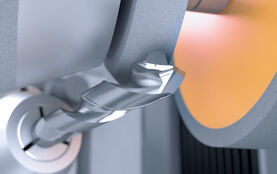
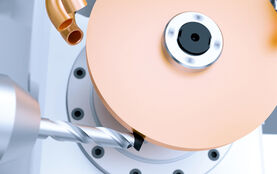
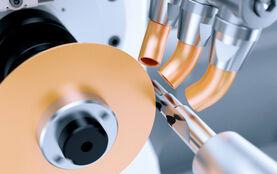
One of the key factors in modern tool production is automating the work processes. For the VHybrid 260 too, VOLLMER has meaningful equipment options with which you can make your production processes more precise, faster and more reliable.
- The HC 4 chain magazine provides space for up to 39 HSK 63 tool holders in a compact design
- Automatic replacement of up to eight grinding or eroding wheel sets, complete with coolant nozzles. Another contribution towards productivity within your manufacturing process
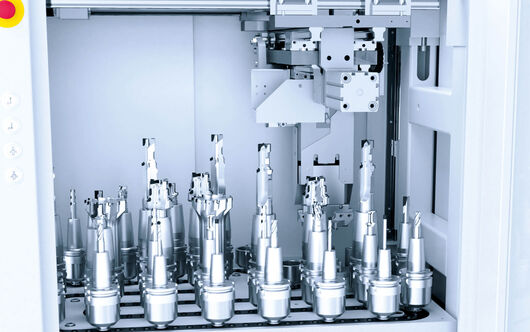
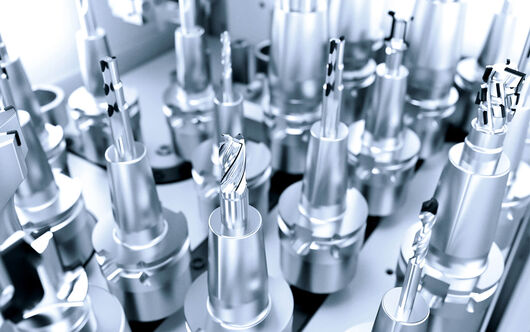
PERFORMANCE PACKAGE
MORE EFFICIENT, MORE ECONOMICAL, FLEXIBLE TO USE.
Our eroding machines have another ace up their sleeve when it comes to efficiency. They can draw on additional power when eroding where appropriate. Use the performance packages for this, currently for the QXD 250 and VHybrid 260 in particular. Depending on the tool geometry and your machining requirements, the use of the performance package can ensure that the machining time is additionally reduced and, therefore, guarantee a significant increase in efficiency for the machine.
However, the performance increase depends on the parameters of the tool to be machined. The performance package is, therefore, completely flexible. If the user wants to use it for a specific tool, they switch it on and then simply switch it off again in the same way when they are finished. The billing model can be flexibly adapted by the customer to their needs via an hourly quota.
The operating concept
A progressive machine demands an equally progressive operating concept. For the VHybrid 260, proven VOLLMER principles were combined with new features. Thanks to the clever positioning of the control desk, users always have a clear view of both the LCD display and the working area. Operation via the touchscreen or keyboard is simple, intuitive and precise as is typical of VOLLMER. The multifunction handwheel for adjusting a desired axis – independent of the control desk – provides even greater flexibility. The newly developed tool manager makes an important contribution to the overall concept, enabling particularly simple handling of grinding wheels and electrodes – and thus helping to further reduce non-productive times. The result: Intuitive and precise operation in every phase of use.
ERGONOMIC OPERATION
- Height-adjustable and tilting control desk
- Optimal machine access
- High-quality LCD display, optimal positioning
- Simple touchscreen control
- Multifunction handwheel for easy axis adjustment
- Simple management of the grinding wheels and rotary electrodes with the VOLLMER tool manager

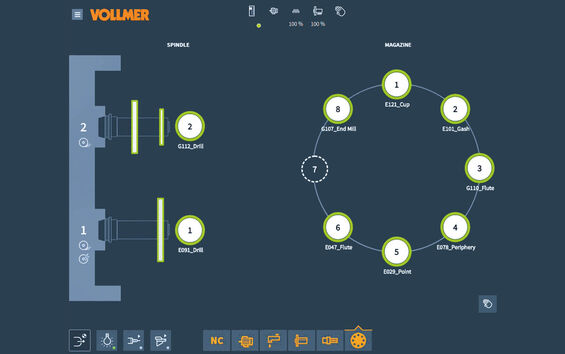
EXLEVEL PRO
The VHybrid 260 is perfectly equipped with the further developed and comprehensive ExLevel PRO software. The modular design enables efficient machining of a wide range of tools in both the grinding and eroding areas, and therefore guarantees quick and easy implementation of all service and production processes. The required simulation can be set up directly at the control desk or at an external programming place.
- Modular design for individual geometry machining
- Simple input and programming
- Quick programme generation through default function
- Simple handling with the tool manager
- Tool simulation in 2D/3D
- Optimal machine monitoring
Your Contact
Josef-Loroch-Str. 1
69509 Mörlenbach
Germany
Phone: +49 6209 71590
Fax: +49 6209 715938
info@loroch.de