We detected, that your browser supports another language than the called one. This page is also available in your language! Would you switch to this page in your language?
Allied Tooling relies on British-German partnership 2024-07-24
to overviewThe British company Allied Tooling has achieved impressive growth over the past decade, more than doubling its turnover. The tool manufacturer's recipe for success is close cooperation with German companies: The British company used machines from sharpening specialist VOLLMER for the high-precision machining of milling cutters, drills and circular saws.
The town of Poole in the south of England is located in the county of Dorset on the coast of the English Channel and has a population of around 150,000. The town is home to the tool manufacturer Allied Tooling, whose rotary tools and circular saws are made of high-speed steel (HSS), carbide (HM) or polycrystalline diamond (PCD) and are used in a variety of industries: Boat builders, kitchen manufacturers, Formula 1 racing teams and aerospace companies use Allied tools to machine metal, wood and composite materials.
In-house PCD machining is a growth driver
Allied was founded in the 1970s and currently employs more than 60 people – in the last six years alone, the tool manufacturer has more than doubled its turnover to over eight million euros. One of the decisive factors for the expansion was the decision to no longer outsource the machining of PCD tools, but to do this in-house.
"HSS and carbide-tipped saw blades had long been established in our company, but the upswing in PCD tools has led to the manufacturing industry recognising that PCD circular saws also offer enormous advantages when cutting highly abrasive materials and machining-intensive applications," explains Wes Hacker, CEO of Allied Tooling. "We have responded to the increased demand in the PCD environment and repositioned ourselves: Today, we carry out PCD machining in-house and have expanded our services for PCD tools."
Partnership with AKE for the United Kingdom
Another factor in Allied's growth was its appointment as the exclusive saw blade partner in the UK for the German tool manufacturer AKE Knebel. AKE is based in the Swabian town of Balingen and is one of the world's leading manufacturers of circular saws and milling tools. As AKE sharpens its saw blades with VOLLMER machines, Allied has invested in further grinding and erosion machines from the VOLLMER Group as part of the AKE partnership. This enables the British company to resharpen even the complex saw blade geometries developed by AKE with high precision during maintenance and servicing. The result is that Allied now services, repairs and delivers more than 1500 AKE saw blades in OEM quality to its customers every week.
"Our partnership with AKE and the investment in several VOLLMER machines have enabled us to significantly increase our level of automation and the quality of our sharpening technologies," says Wes Hacker. "This has enabled us to double our sales of carbide tools over the past five years – and we have even been able to increase our growth by a factor of five in the PCD area."
VOLLMER erosion machines make the difference
The VOLLMER Group supplied the first grinding machines to Allied back in the 1990s. Since then, more than 20 machines have found their way from Swabia across the English Channel to Poole. The company's entry into PCD machining has meant that Allied has purchased two VOLLMER QXD 250 disc erosion machines, a VPulse 500 wire erosion machine and a QM eco select disc erosion machine since 2018. With the automated Vollmer HC 5 chain magazine, Allied can use the QXD 250 around the clock and via unmanned operation.
"We bought the VPulse 500 wire erosion machine in particular because of its enormous flexibility," says Wes Hacker. "The simultaneous five-axis kinematics and the polymer concrete base provide us with unrivalled precision in PCD machining. Thanks in particular to the thin eroding wire, we can sharpen even complex areas of a tool with a quality that we could not achieve with an eroding wheel."
Sharpening circular saws with machines from Loroch and VOLLMER
For the machining of circular saws, Allied's 16,000 square metre production hall houses over a dozen sharpening machines from VOLLMER and Loroch – a subsidiary of the VOLLMER Group. Allied uses the Loroch KBN and KSC machines primarily to grind high-speed steel circular saw blades. The British company uses several VOLLMER grinding machines from the CHD and CHX series to sharpen carbide-tipped circular saws. The CHD 270 grinding machine delivered in October 2021 alone enabled Allied to increase its production capacity for carbide-tipped circular saws by more than 30 per cent. The reason for this is the faster processing speed and the high degree of automation of the CHD 270. This is not only due to the ND 340 handling system, but also to functions such as acoustic sensors and the measuring cube for inspection and recalibration during the sharpening process. In addition, the CHD 270 with its new drive systems and programming interfaces enables the use of multi-path software and complex saw blade designs.
In January 2024, Allied expanded its machine fleet with the QM eco select erosion machine for machining PCD circular saws. It offers Allied the possibility of machining tools and saws with PCD up to a diameter of 600 millimetres. It can be used to erode both the back and flanks of PCD-tipped saw teeth. Allied also uses its QR 270 erosion machine for finishing sawtooth tips.
"Allied Tooling, AKE Knebel and the VOLLMER Group are a good example of how economic cooperation between the UK and Germany can be extremely worthwhile," says Andreas Böhm, CEO of the VOLLMER Group. "All three companies are SMEs, and it is precisely this level of equality on which we meet that is the key to our joint success and corresponds to our ideas of how we want to drive forward our internationalisation in the future."
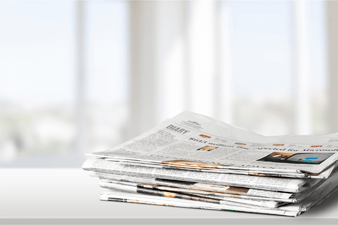
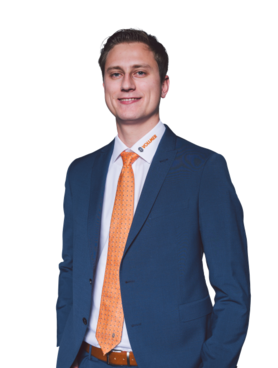
Your Contact
VOLLMER WERKE Maschinenfabrik GmbH88400 Biberach/Riß
Germany